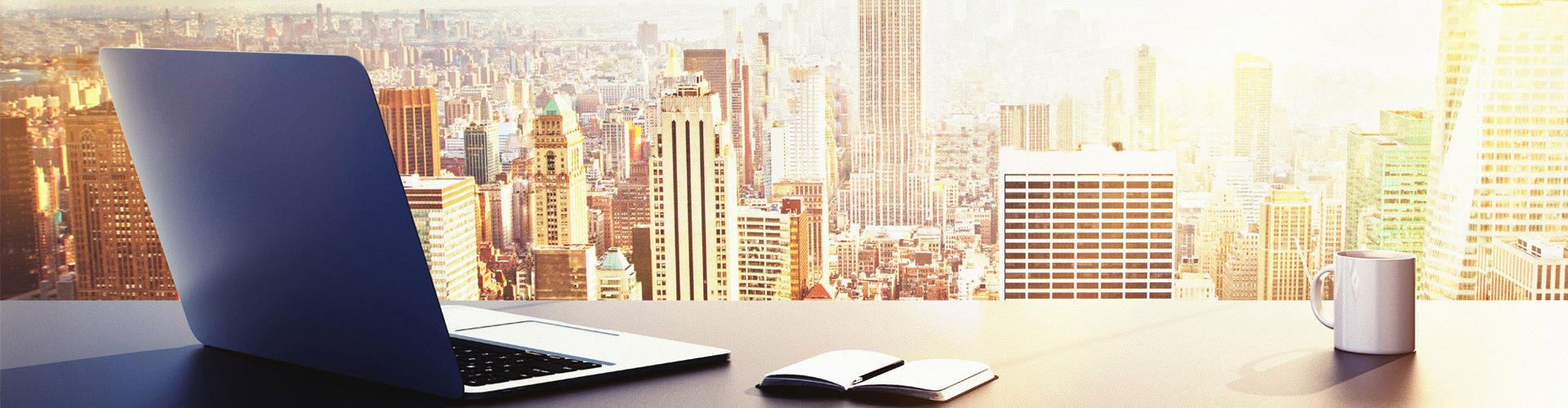
資訊分類
飼料加工中熱敏物質的損失及後添加解決工藝討論
- 分類 :行業聚焦
- 作者 :
- 來源 :
- 發布時間 :2022-11-17 09:41
- 訪問量 :
【概要描述】影響熱敏物質活性的加工工序維生素 、酶製劑和益生菌作為高效飼料添加劑 ,已日益為人們所重視 ,但應用效果不一 ,原因是在應用過程中使其破壞的因素太多 。目前飼料加工工藝中對酶製劑起破壞作用的主要是製粒和膨化工序 。1.製粒工序在製粒過程中 ,需要加入4%-5%的蒸汽進行調質 ,使物料升溫至50℃左右 。粉料在調質器中滯留15s以上 ,最少也不低於6s 。另外 ,物料與壓輥 、壓模與模孔之間的摩擦 ,也可升溫5一20℃ ,從而使
飼料加工中熱敏物質的損失及後添加解決工藝討論
【概要描述】影響熱敏物質活性的加工工序維生素 、酶製劑和益生菌作為高效飼料添加劑 ,已日益為人們所重視 ,但應用效果不一 ,原因是在應用過程中使其破壞的因素太多 。目前飼料加工工藝中對酶製劑起破壞作用的主要是製粒和膨化工序 。1.製粒工序在製粒過程中 ,需要加入4%-5%的蒸汽進行調質 ,使物料升溫至50℃左右 。粉料在調質器中滯留15s以上 ,最少也不低於6s 。另外 ,物料與壓輥 、壓模與模孔之間的摩擦 ,也可升溫5一20℃ ,從而使
- 分類 :行業聚焦
- 作者 :
- 來源 :
- 發布時間 :2022-11-17 09:41
- 訪問量 :
詳情
影響熱敏物質活性的加工工序 維生素
、酶製劑和益生菌作為高效飼料添加劑
,已日益為人們所重視
,但應用效果不一
,原因是在應用過程中使其破壞的因素太多
。目前飼料加工工藝中對酶製劑起破壞作用的主要是製粒和膨化工序
。 1.製粒工序 在製粒過程中
,需要加入4%-5%的蒸汽進行調質
,使物料升溫至50℃左右
。粉料在調質器中滯留15s以上
,最少也不低於6s
。另外
,物料與壓輥
、壓模與模孔之間的摩擦
,也可升溫5一20 ℃
,從而使製粒後顆粒溫度達到70~90 ℃
,甚至100 ℃左右
。 2.膨化工序 在擠壓膨化工藝中
,溫度可高達 130~160 ℃
,但是飼料在如此高的溫度下的滯留時回很短(5~10 s)
。在加工浮性水產飼料時
,蒸汽和水的添加量達8 %
。擠出物通過模頭時的最終壓力為3.45~4.0 MPa
,溫度為 125~138℃
,水分25 %一27%
。 熱敏物質在飼料加工中的損失 1.維生素的損失 維生素具有不飽和碳原子
、雙鍵
、羥基或對物理與化學因素非常敏感的結構
,調質過程中的高溫處理以及較長時間的擠壓導致溫度急劇上升
,都會造成維生素活性降低(Lobo
,2001)
。Michael (2001)研究了不同製粒工藝參數下維生素的保存率
,結果發現
,隨著製粒溫度的上升和製粒時間的延長
,各種維生素的存留量隨之下降
。 王紅英等(2004)的研究結果表明
,隨著製粒溫度的上升
,維生素C的保存率隨之下降
,當製粒溫度為90℃時
,保存率隻有56%
。當壓力為0.55MPa時
,保存率最低為60 %
。BASF公司對飼料中維生素損失及 ROCHE公司於1991年對英國主要飼料廠顆粒飼料加工過程中不同維生素損失的實測結果(製粒溫度為70~90 ℃)見表1
。 
2.酶製劑的損失 飼料加工中的調製﹑製粒及膨化均容易使酶類變性失活
。一般酶活性的最適溫度為30—45℃
,超過60℃時酶就會變性
,喪失活性
。製粒膨化過程中
,大多數酶製劑的活性都將喪失殆盡
。史清河(2000)研究表明
,製粒溫度為79 ℃時
,植酸酶活性下降45.8.%
,8O ℃時則下降87.5 %
。鄧君明等(2002)研究表明
,75 ℃和 95℃的製粒溫度
,可使β-葡聚糖酶的活性分別降低40 %和70 %
,當溫度超過110 ℃時β-葡聚糖酶和纖維素酶活性全部喪失
。木聚糖酶在75
、85和95℃溫度條件下
,處理5min
,製粒後酶活性的損失率分別達到15.58 %
、24.54 %和59.96 %
;處理10 min
,酶活性的損失率分別為 19.80 %
、27.40 %和61.93 %
。 以大麥和小麥為主要原料的豬飼料在膨化加工後
,其中熱敏性較高的植酸酶在經過各個加工工序的相對活性如表2所示: 表2 膨化加工過程中植酸酶的相對活動 
3.益生菌的損失 益生菌的本質是活性微生物或其培養物﹐對溫度
、壓力
、氧氣等比較敏感
。製粒膨化過程中的溫度可達到100~200 ℃
,並伴有高濕(容易使物料升溫)
,高壓現象
,且氧含量低(對需氧杆菌損害尤其大)
,在該條件下大多數益生菌的活性都將受到不同程度的影響
。 溫度對益生菌的影響尤為明顯
,乳酸杆菌類益生菌
,在65~75℃下致死
。芽孢杆菌類益生菌由於含有芽孢
,能耐100 ℃的高溫
,但飼料製粒膨化過程中可以產生高於100 ℃的溫度﹐所以加工對芽孢杆菌的活性仍然存在一定影響
。氧的含量主要影響需氧益生菌如大多數芽孢杆菌類益生菌的活性
。加工過程產生的缺氧狀態必然減少芽孢杆菌數量
,並影響其作用效果
。徐海燕等(2005)研究表明
,添加了益生菌的顆粒料經過高溫製粒後
,活菌損失率在5 %~10 %之間
。 防止熱敏物質損失的解決方案
:後添加工藝 1.不同的後添加方法 1.1直接添加懸浮液或膠體 Kvanta1987年報道將含有少量生物活性的物質(包括維生素﹑酶製劑﹑微生物製劑等)結合到製粒後的飼料中
,將含有生物活性的物質先與一種惰性物質載體混合成液體
,形成均勻的懸浮液
,懸浮液再通過一種設備轉化為一種可作用於粒料的形態,形成均勻的一層薄膜覆蓋於粒料的表麵
。 Lavery1996年也報道了一種添加酶製劑等組分到顆粒中的方法
:將添加物質與一種粘性膠體混合後
,再與飼料顆粒混合
。這種覆蓋膠體的顆粒基本上是均勻的
,對混合機的汙染也很小
,它的添加量約為2~40kg/t
。這兩種添加方法
,比較適合於小批量生產飼料或農場自行加工
。 1.2噴霧添加液體 國外幾種比較有代表性的液體添加係統如下
: 德國Amandus Kahl 公司是開發後置添加技術的先行者
,其液體添加係統的核心是旋轉噴霧添加機
。據資料介紹
,當用於添加植酸酶時
,液體分布的均勻度變異係數小於10 %
;當顆粒料的流量為5~20t/ h時,液體料噴在顆粒飼料上的達98 %以上
。 比利時的Schranwen公司與美國的Finn-feads 公司聯合開發了新型噴塗—添加係統
。該係統通過一台泵將液態的酶製劑以經過計量的流速送至氣助霧化噴嘴
,噴嘴位於旋轉圓盤的上方
,這個圓盤從一個衝擊式稱量器中接收顆粒飼料
,並能使物料在其上麵停留大約30s
。由於圓盤的轉動
,再加上有一個槳輪對顆粒飼料的不斷翻動
,因而所有的顆粒都能被噴塗
。 丹麥 Sprout-Matador公司於1999年開發了微量液體添加係統
,該係統主要用於添加酶製劑等微量液體組分到顆粒上
。該係統的噴塗劑量能夠達到每1t飼料10g
,並且其變異係數(CV)小於10 %
。 2.後添加點的選擇 顆粒未冷卻時添加酶製劑等熱敏性微量組分
,也會造成熱敏性組分的損失
。後添加點一般選擇在顆粒冷卻後
,可供選擇的有3處
。 (1)噴油設備
:有的飼料廠本身備有油脂包埋器
,加裝噴液係統不需要修改工藝流程
。 (2)螺旋輸送機
:采用在螺旋輸送機上安裝噴液的辦法
,可節省設備成本投入
;不足之處是混合均勻效果差
,變異係數一般大於20 %
。 (3)液體噴塗機
:這類設備一般安裝在顆粒冷卻器後
。 3.後添加工藝的關鍵點 3.1連續計量的準確性 同常規的添加一樣
,後添加組分的精確添加對產品的質量至關重要
。供料係統的不精確
,噴液係統的計量不準或供料係統與嗩液係統比例相互不一致都將導致添加量的誤差
,對最終產品質量產生不良影響
。 3.2後添加液體組分分布的均勻性 後添加液體組分的混合均勻度是評價後添加設備質量好壞的關鍵指標之一
,其均勻度變異一般以小於7 %為好
。 3.3後添加組分體係的穩定性 對於單個顆粒而言
,傳統的添加(原料混合前添加)能使組分均勻分布於顆粒內部﹐而後添加則使添加組分集中於顆粒表麵。因此附著在表麵的液體必須考慮到以下二方麵的穩定性
:①表麵粘附的穩定性
。由於飼料在包裝或運輸等過程中都有可能造成對顆粒的破壞
,提高飼料的含粉率
,從而使液體組分比較集中於細粉中
。這種變化不僅導致液體組分分布不均
,還可能對動物產生不良影響﹐因此要求液體成分能牢固地附著在固體顆粒的表麵
。②表麵自身的穩定性
。後添加液體組分集中於顆粒表麵後更易受環境因子
,如溫度
、光
、氧氣及濕度等影響
,從而導致在貯藏過程中這些組分的損失比普通料中的損失更快
。因此要求這些液體成分有更好的自身化學穩定性
。 (文章來源
:寵物食品聯盟)
關鍵詞
:
掃二維碼用手機看
上一個:
無
下一個:
2020年中央一號文件來了(內附全文)
上一個:
無
下一個:
2020年中央一號文件來了(內附全文)
Copyright ©鼎點平台農牧科技集團公司保留所有版權